Product Architecture and Strategy
- Vehicle Upstream Definition and Engineering.
- Vehicle Packaging Study For New and Existing
- Feature List and Confirmation.
- Definition of Master Section and Gap and Flush Targets.
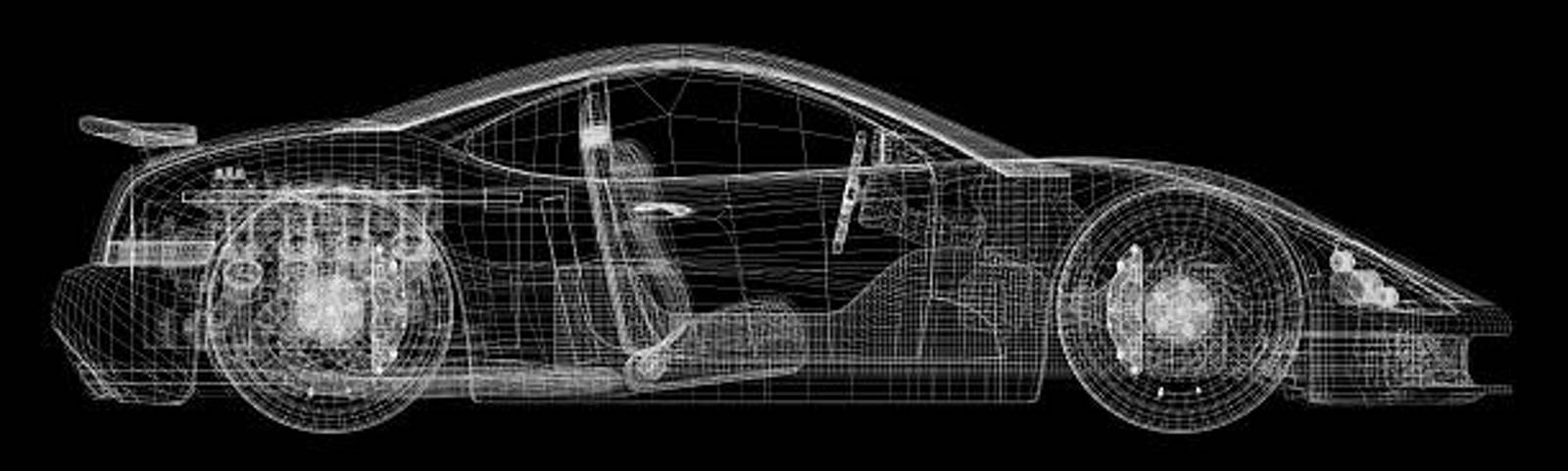
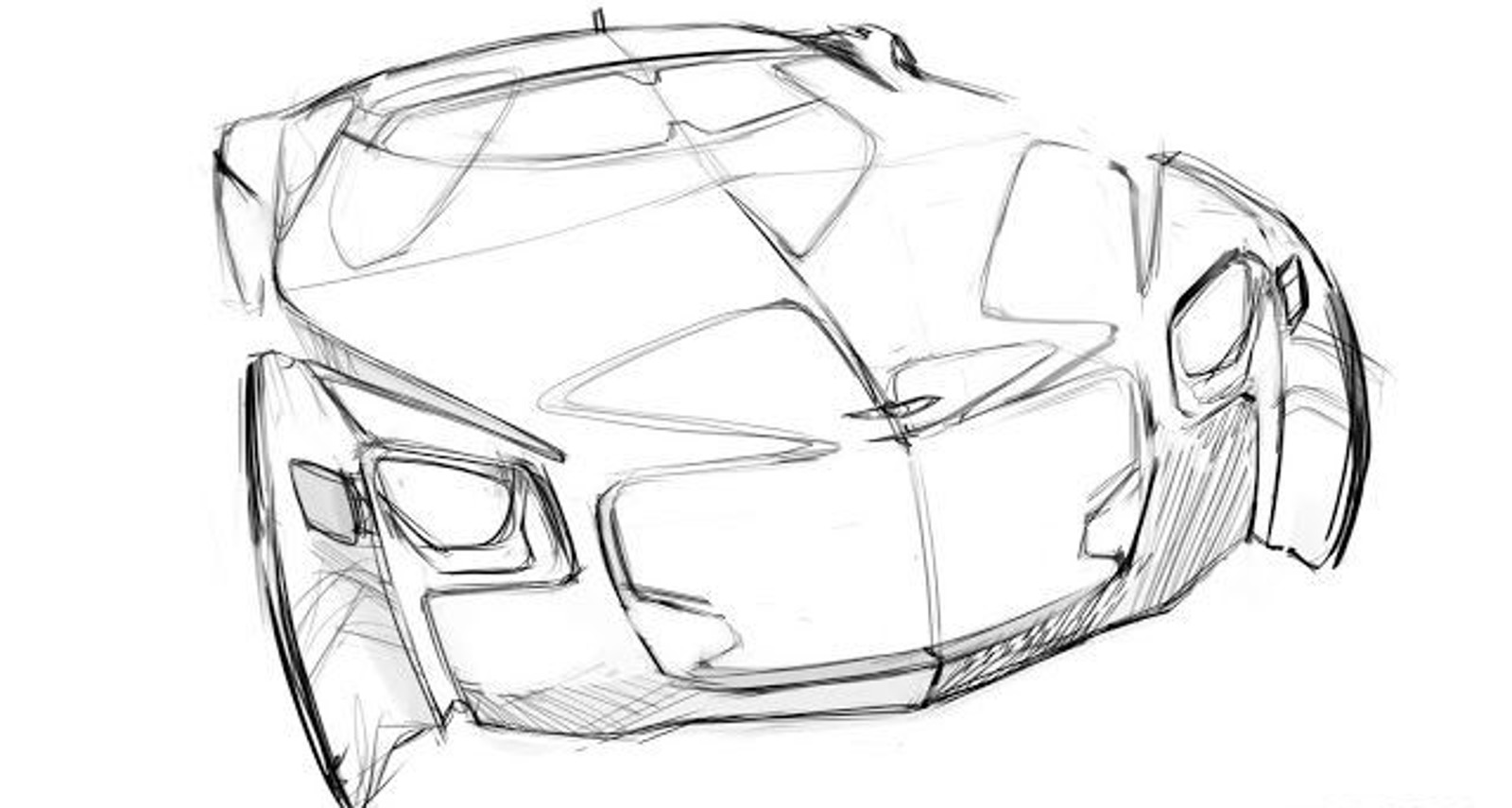
Product Engineering Design and Development
- Concept Development
- Detailed Design
- Product Variants
- Design Validation / Support Tolerance Analysis
- Assembly Validation
- Value Engineering
- Cost-Optimization Analysis
- Reverse Engineering
- DFX Manufacturability, Power, Variability, Cost, Yield or Reliability
- DFMEA (Failure Mode Effect & Analysis)
- Design Data Migration
CAD/ CAE / FEA / Simulation-Team & Capabilities
Ingstron’s teams collaborate with customers to test, validate, and conduct packaging & feasibility studies, ensuring strict safety compliance. Their multidisciplinary teams work seamlessly to certify components, with successful homologation for the US market.
CAD Resources | CAE Capabilities | CAE Software |
|
|
|
Expertise In:
- BIW–Body structure
- Closures–Doors, Hood, Trunk
- Exterior–Windshield, Bumper, etc.
- Trim-Interior & Exterior
We have the resources, expertise, processes, and data sets to engineer your needs. Contact us.

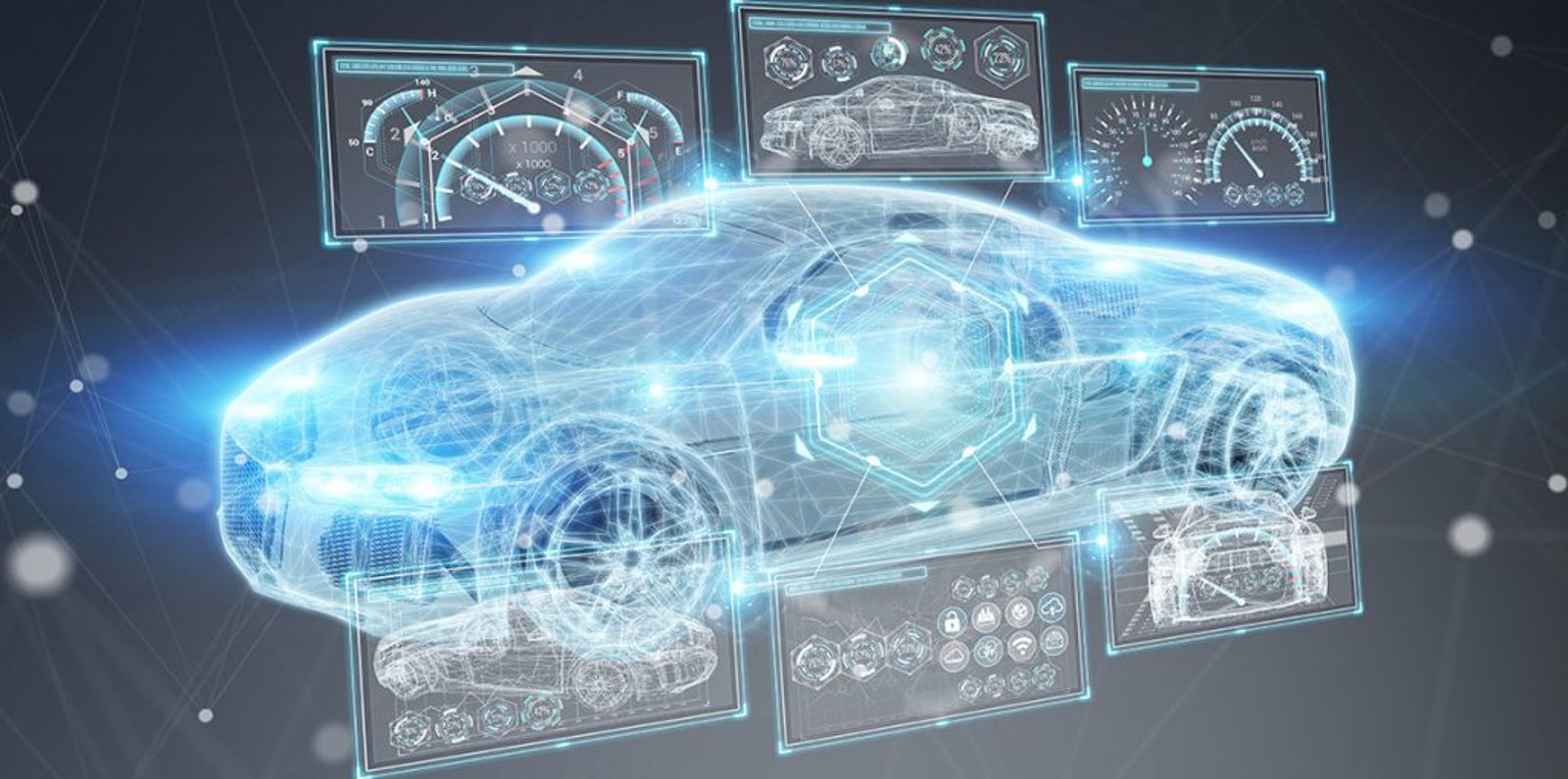
Product Virtual Validation
Virtual validation uses simulation to test vehicle performance, safety, and functionality, reducing costs and development time. It involves creating computer (FEA/CAE) models of vehicle components (engine, chassis, electrical systems) to assess performance and identify improvements without physical prototypes.
Product Testing
- Product Performance Target Setting
- Virtual Analysis of Durability, NVH and Drivability
- Confirmation of Regulatory Requirements
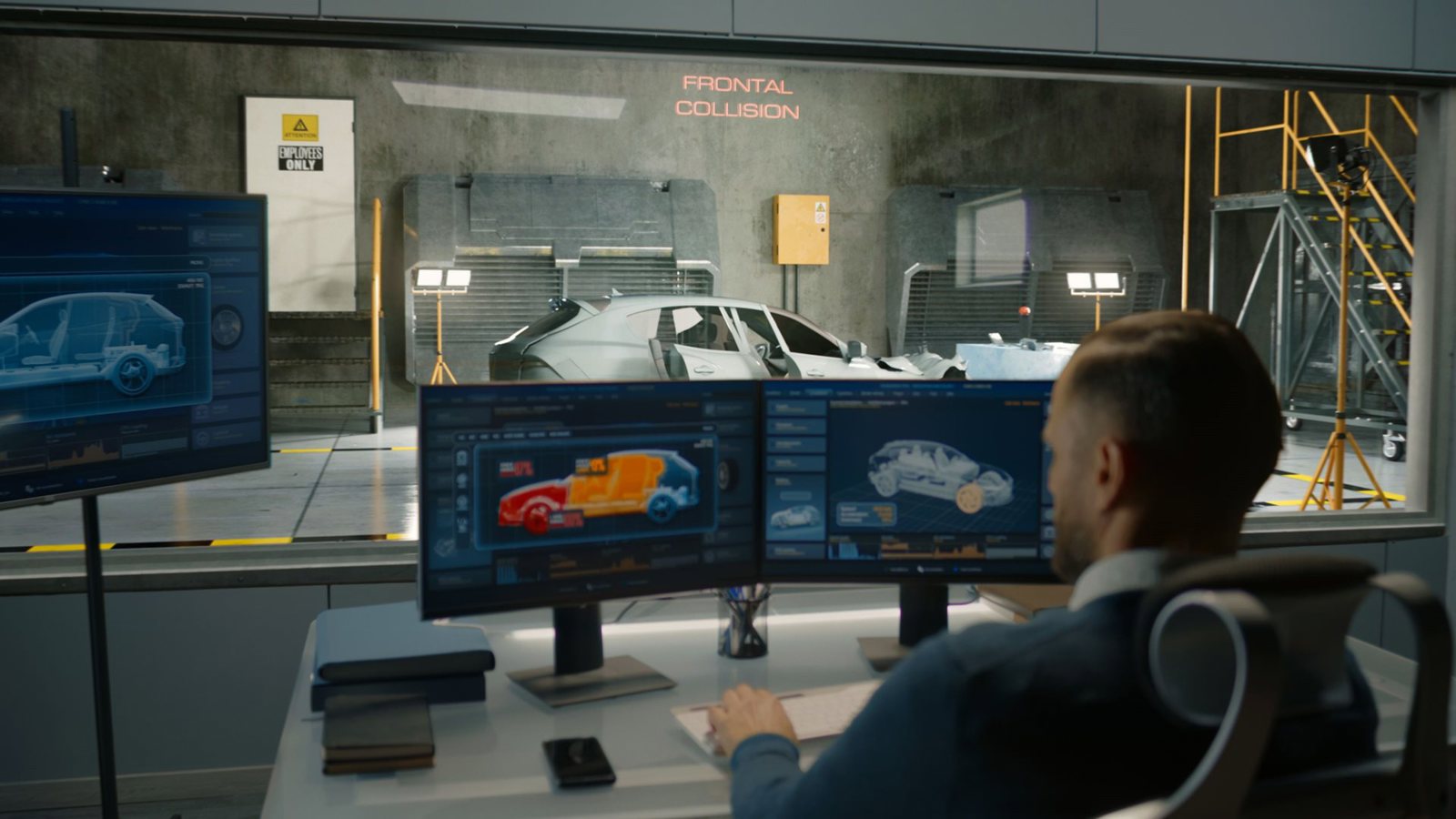
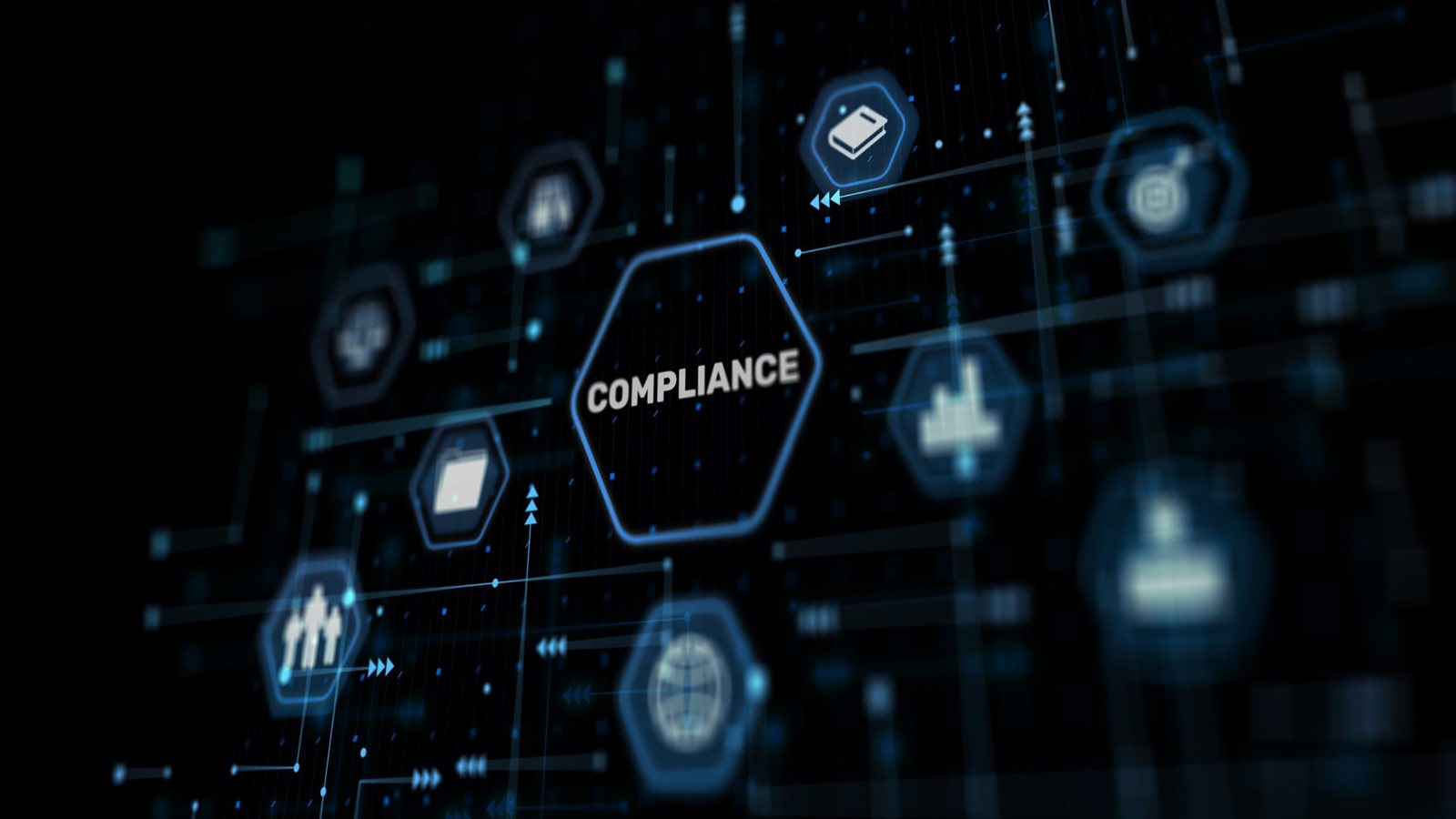
Product Localization
- Region-Specific Regulatory Requirement Identification.
- Supplier Identification and Tool Adaption.
- Equivalent Material Definition
- Process Adaption